bearing superfinishing process
Ultra precision technology is not only used in the bearing industry, but also in the engine. This technology is also used in other precision machinery and instruments.
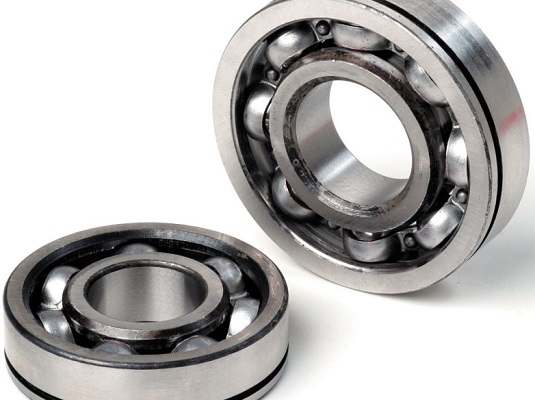
What is bearing superfinishing?
Bearing superfinishing process is a finishing method to realize micro grinding by feeding movement.
The surface before superfinishing is usually precision turned and ground. Specifically, it refers to a finishing method in which a fine-grained abrasive tool (oilstone) is used to exert a small pressure on the workpiece under good lubrication and cooling conditions, and a fast and short reciprocating oscillation motion is made for the workpiece rotating at a certain speed in the direction perpendicular to the rotation direction of the dry workpiece.
What is the function of bearing superfinishing?
In the manufacturing process of rolling bearing, super precision is the last process of bearing ring processing. It plays an important role in reducing or eliminating the circular deviation left by grinding, repairing the shape error of channel, refining its surface roughness, improving the surface physical and mechanical properties, reducing the vibration and noise of bearing and improving the mission of bearing.
It can be embodied in the following three aspects
1. It can effectively reduce the waviness. In the process of superfinishing, in order to ensure that the oilstone always acts on the wave crest and does not contact the wave trough, the arc of the oilstone in contact with the workpiece is ≥ the wavelength of the waviness of the workpiece surface. In this way, the contact pressure of the wave crest is large, and the convex peak is removed, so as to reduce the waviness.
2. Improve the groove error of ball bearing raceway. Superfinishing can effectively improve the groove error of raceway by about 30%.
3. It can produce compressive stress on the superfinished surface. In the process of superfinishing, cold plastic deformation is mainly produced, so that residual compressive stress is formed on the workpiece surface after superfinishing.
4. The contact area of the working surface of the ferrule can be increased. After superfinishing, the contact bearing area of the working surface of the ferrule can be increased from 15% ~ 40% to 80% ~ 95%.
Bearing superfinishing process:
1. Bearing cutting
When the grindstone surface is in contact with the convex peak of the rough raceway surface, due to the small contact area and the large force per unit area, under a certain pressure, the grindstone first receives the “reverse cutting” effect of the bearing workpiece, so that part of the abrasive particles on the grindstone surface fall off and break, exposing some new sharp abrasive particles and edges. At the same time, the convex peaks on the surface of bearing workpiece are subject to rapid cutting. The convex peaks and grinding metamorphic layer on the surface of bearing workpiece are removed by cutting and reverse cutting. This stage is called the cutting stage, in which most of the metal surplus is removed.
2. Half cutting of bearing
As the machining continues, the surface of the bearing workpiece is gradually ground flat. At this time, the contact area between the grindstone and the workpiece surface increases, the pressure per unit area decreases, the cutting depth decreases, and the cutting capacity decreases. At the same time, the pores on the surface of the grindstone are blocked and the grindstone is in a semi cutting state. This stage is called the half cutting stage of bearing finishing. In the half cutting stage, the cutting marks on the surface of bearing workpiece become shallow and appear darker luster.
3. Finishing stage
This stage can be divided into two steps: one is grinding transition stage; The second is the grinding stage after stopping cutting
Grinding transition stage:
The self sharpening of abrasive particles decreases, the edge of abrasive particles is smoothed, the chip oxide begins to embed into the gap of oilstone, and the abrasive powder blocks the pore of oilstone, so that the abrasive particles can only be cut weakly, accompanied by extrusion and polishing. At this time, the surface roughness of workpiece decreases quickly, and black chip oxide is attached to the surface of oilstone.
Stop cutting and grinding stage:
The friction between the oilstone and the workpiece has been very smooth, the contact area has greatly increased, the pressure has decreased, and the abrasive particles can no longer break through the oil film to contact the workpiece. When the oil film pressure on the bearing surface is balanced with the oilstone pressure, the oilstone will float. An oil film is formed between them, which has no cutting effect at this time. This stage is unique to superfinishing.